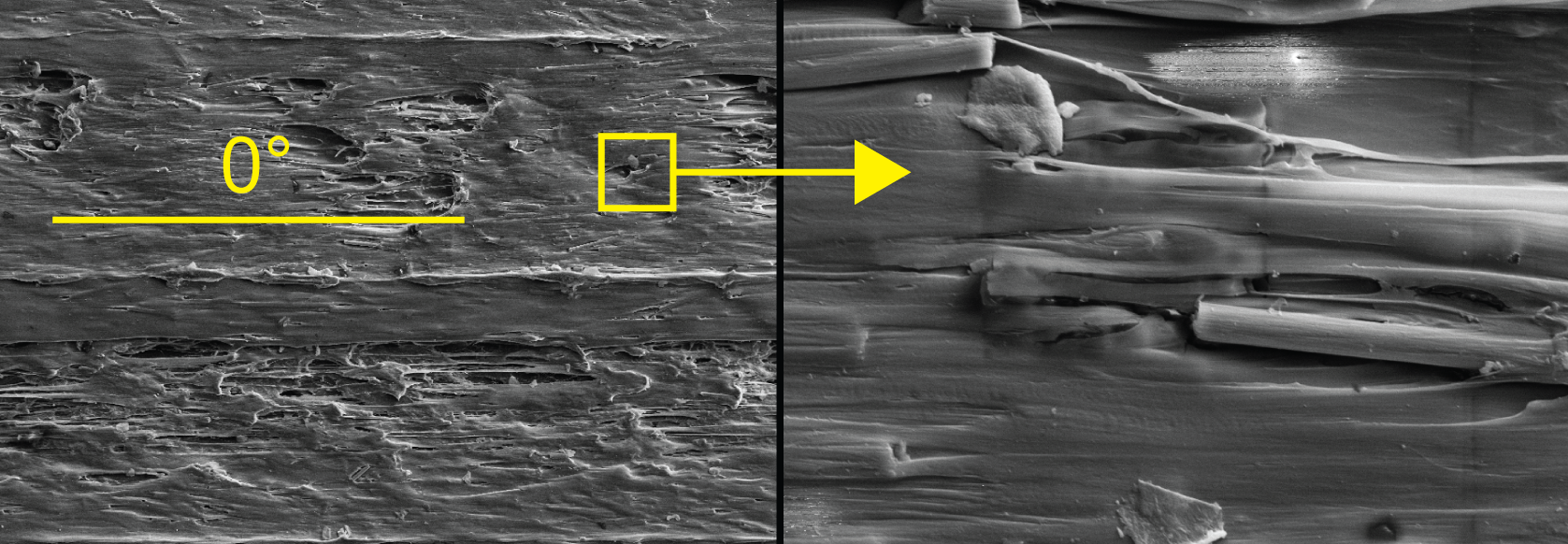
Material Characterization of Fiber-reinforced thermoplastic materials
Fiber-reinforce thermoplastic bilayer actuator design
The workflow of iterative 4D printing design. (A) shows the structure of a block with PLA as an actuator and CFPLA as constraint. (B) shows the process of material characterization based on DMA experiments. (C) refers to the FEA modeling on a bending unit. (D–E) show the iterative design process based on the simulation. This iterative process yields the finalized design, and leads to fabrication
Microscale view of PLA material and block structure with different functional components
(A) The polymer chain inside the 3D printed PLA structure. (B) Anisotropic blocks consisting of two layers with different printing path directions: the actuator blocks (white) and the constraint blocks (gray). (C) Bending unit with actuators (white) and constraints (gray). (D) The process from programmed printing path to fabricated flat piece and triggered bending unit.
Experiment results of three types of thermoplastic materials
PLA, CFPLA, and PLA–CFPLA composite bi-layer blocks, with varying layer thicknesses from 0.1 mm to 0.5 mm. Results show that PLA bending units have the largest bending deformation while CFPLA bending units have the smallest bending deformation
SEM images of CFPLA
(A–B) show zoom-out and zoom-in pictures of the sample with the printing direction of 0◦. (C–D) show zoom-out and zoom-in pictures of the sample with the printing direction of 45◦.